Manifold valves are crucial components in many industrial applications involving pressure measurement instruments, offering numerous advantages in terms of efficiency, safety, and control. Let’s explore the main types of valves, their functions, and the key benefits they provide.
Fundamentally, Manifold used in industrial applications with pressure gauges, pressure switches, transducers, and transmitters are a type of process connection system that provides isolation, venting, and equalization for various types of pressure measurement applications. Almost all pressure measurement instruments operate in conjunction with a valve or a combination of valves, whose reliability is critical for the safety of the entire plant. Therefore, it is highly important to strategically select the most suitable manifold valve for the specific application. Choosing a high-quality valve is essential not only to ensure accurate pressure measurement but also to prevent hazardous leaks, damage to equipment, and risks to operational personnel, especially in the presence of high-pressure surges.
Manifold are categorized into different types, each with specific characteristics and applications. Here is a brief overview of the most common ones:
Two-way Manifold
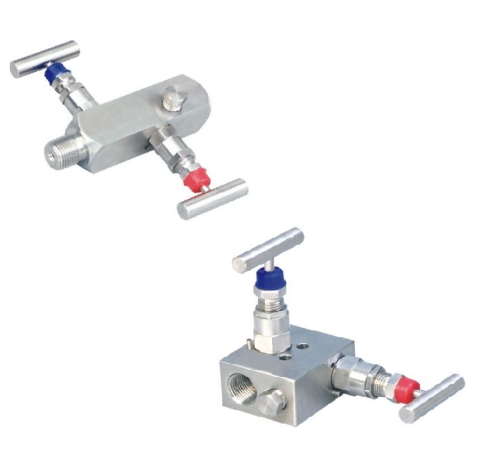
These are the simplest valves, designed to work with most pressure devices and used to allow or block fluid flow. They consist of a block valve and a vent valve. They are widely used in basic measurement systems where monitoring a single pressure point is necessary. They prevent initial pressure surges and allow for venting, bleeding, and calibrating instruments without physically removing them from the process. This type of valve also allows for isolating the instruments from the process, enabling the safe removal of instruments for maintenance or sostitution.
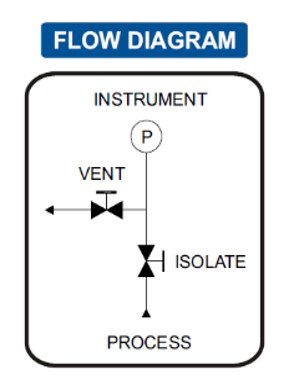
Three-way Manifold
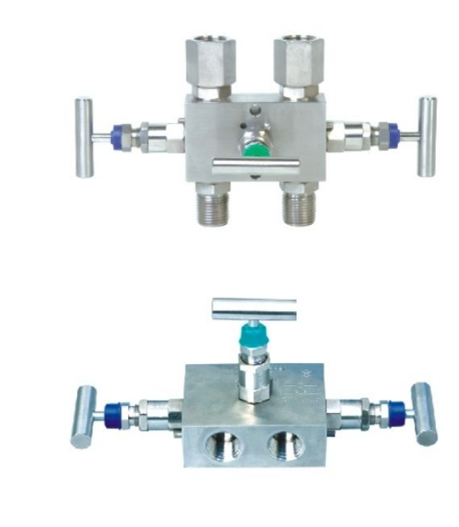
Three-way Manifold have a more complex configuration compared to the previous ones. Consisting of two block valves and one equalizing valve, they allow for the connection and control of two different pressure lines with a single instrument. Three-way Manifolds are used with differential pressure gauges, pressure transmitters, and pressure switches. They prevent installation pressure surges by equalizing the high and low-pressure ports, and they isolate the process, allowing the instrument to be removed without the need to shut it down.
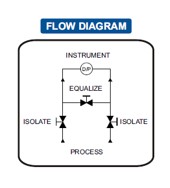
Five-way Manifold
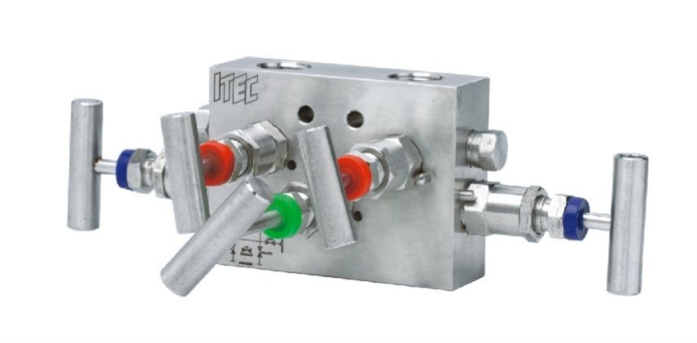
These are the most complex valves, equipped with five ports for connection to multiple pressure lines and instruments, allowing for draining, calibration, and the simultaneous connection of multiple pressure measurement instruments. Five-way manifold valves typically consist of two block valves, one equalizing valve, and two vent or test valves. Like the previous ones, they are used with differential pressure gauges, pressure transmitters, and pressure switches. They prevent installation pressure surges by equalizing the high and low-pressure ports and isolate the process, allowing the instrument to be removed without the need to shut it down.
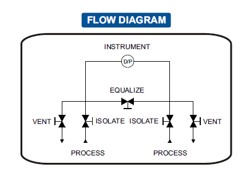
Function of Manifold and Usage Advantages
Precise pressure control and regulation: one of the main advantages of using manifold valves in combination with pressure gauges is the ability to precisely monitor and regulate pressure within a system. This is particularly important in industries such as chemical, petrochemical, and food processing, where maintaining pressure within specific limits is crucial for product quality and process safety.
Enhanced safety: safety is a priority in any industrial plant. Manifold used with pressure gauges help enhance safety by reducing the risk of overpressure and leaks. Additionally, these valves can be designed with extra safety features, such as relief valves and locking devices, which help prevent hazardous situations.
Operational efficiency: using Manifold improves the operational efficiency of plants. By constantly monitoring pressure and making precise adjustments, downtime and process interruptions are minimized. Preventive maintenance becomes easier as pressure gauge readings can indicate when a valve needs maintenance or replacement, thereby avoiding sudden failures and costly production halts.
Cost savings: the ability to accurately monitor and regulate pressure reduces energy and material consumption, improving overall process efficiency. Additionally, preventing failures and reducing downtime lowers maintenance and repair costs.
Ease of installation and maintenance: Manifold are designed for easy installation and maintenance. Many models feature standard fittings and can be easily integrated into existing systems. The availability of modular accessories and components further simplifies installation and maintenance, allowing operators to quickly replace defective parts without dismantling entire systems.
Application versatility: Manifold are extremely versatile and can be used in a wide range of applications. Their ability to operate under different pressure and temperature conditions makes them suitable for various industrial sectors, offering a flexible and reliable solution for pressure control.
Conclusion
Manifold with pressure gauges offer a range of advantages that make them indispensable in many industrial applications. From enhancing safety and operational efficiency to cost savings and ease of maintenance, these valves are an excellent choice for anyone looking to optimize their plant’s performance. Investing in these components can lead to significant long-term benefits, ensuring safe, efficient, and continuous operation.