Pressure gauges are essential instruments in many industrial and process applications, used to measure the pressure of gases and liquids in various contexts. However, there is often an overlooked detail that can significantly affect the accuracy and reliability of these devices: liquid filling. In this article, we will explore the importance of this often-underestimated aspect.
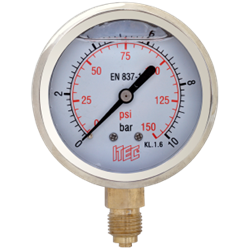
Despite pressure gauges being fundamentally robust mechanical instruments, they can malfunction with prolonged exposure to various conditions such as vibrations, mechanical pulsations, temperature spikes, pressure, and humidity, adverse environmental conditions.
Liquid-filled gauges, usually filled with glycerine or silicone oil, perform better in non-ideal conditions and provide the following advantages:
Vibration and pulsation protection: Liquid filling in pressure gauges provides an important damping function for vibrations and pulsations. This is crucial in industrial environments where operating conditions can be extreme and unstable; the liquid inside the gauge reduces the effect of sudden pressure oscillations, thus protecting the device and improving its long-term durability.
Temperature stabilization: Another advantage of liquid filling is the ability to stabilize the internal temperature of the gauge. This is particularly important in environments subject to extreme temperature variations. The liquid acts as a thermal regulating medium, reducing the effects of temperature fluctuations on the gauge reading reliability.
Minimization of reading errors: Without adequate liquid filling, pressure gauges can be subject to reading errors due to phenomena such as condensation, air bubble formation, or friction effects on the internal mechanism. The liquid provides a constant and homogeneous interface for pressure transmission, minimizing the possibility of measurement errors.
Protection against damage from aggressive media: In cases where gauges are used to measure the pressure of aggressive or corrosive fluids, liquid filling can offer additional protection to the measurement system. The insulating liquid creates an effective barrier between the aggressive fluid and the gauge internal components, thereby extending its lifespan and ensuring greater operational safety.
Increased accuracy and repeatability: Liquid filling contributes to improving the accuracy and repeatability of gauge measurements. By eliminating or minimizing external variables that could influence the readings, more accurate and reliable results are obtained, essential for ensuring optimal operation of industrial processes.
The filling liquids used in pressure gauges must possess certain characteristics to ensure optimal device operation. When choosing the filling liquid for a gauge, it is important to consider several factors such as chemical compatibility, process operating temperature, thermal stability and viscosity, cost, and availability.
Glycerine: Glycerine is one of the most common filling liquids for gauges. It has low viscosity and good vibration damping capacity, as well as good resistance to temperature variations. It is suitable for general applications where particularly high chemical resistance is not required and, in general, is used at moderate temperatures, not lower than -10 ˚C if pure and not lower than -20 °C if mixed with water.
Silicone oil: Silicone oil filling is known for its thermal and chemical stability. It is the preferred filling fluid for very low temperatures, down to -40 °C, and is particularly suitable for high-temperature applications or in the presence of aggressive fluids. Silicone is also resistant to oxidation and degradation, making it a reliable choice for corrosive environments.
Halocarbon oil: This type of oil is used in applications requiring superior chemical resistance, such as those involving highly corrosive fluids. Known for its thermal stability and low volatility, and being chemically inert, it is a good choice for use near oxygen, chlorine, and other reactive gases.
In conclusion, liquid filling of pressure gauges plays a fundamental role in ensuring the reliability and accuracy of these important measuring instruments and brings numerous advantages:
Long-term cost savings: Filling liquid acts as a lubricant for the instrument mechanism, prolonging its life and reducing unplanned plant shutdown costs, thereby extending the instrument’s lifespan.
Reduction of failures: Filling, by protecting the instrument mechanism from strong vibrations, pulsations, and extreme conditions, prevents its breakage.
Ease of reading: In the presence of filling liquid, the absence of condensation and the contained fluctuation of the index make reading easier.